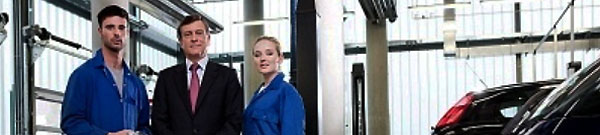
1. Construction
The shift and select lever shaft are set at right angles to the fork shafts on top of the transaxle case. A double-meshing prevention mechanism and reverse gear mis-shift prevention mechanism are adopted. Also, a shift detent mechanism and reverse detent mechanism are adopted on the shift fork shaft.
2. Double-meshing prevention mechanism
This mechanism prevents possible shifting into two gears at the same time. When two shift forks are moved at the same time, they catch during selecting and the gears are doublemeshed. As a result, the gears do not turn, the vehicle acts as though the brakes have been jammed on, and the tires lock up causing a very dangerous situation. The shift fork lock plate is prevented turning by a bolt which allows the shift and select lever shaft to slide only in the select direction.
3. Operation of double-meshing prevention mechanism
The shift fork lock plate fits into two of the three shift fork head slots at all times and locks all shift forks except for the gear to be used. For example, when the shift lever is put into 1st or 2nd gear, the shift fork lock plate and shift inner lever No. 1 move to the right as shown in the diagram on the left. The shift fork lock plate prevents the 3rd/4th and 5th/reverse shift fork heads from moving so that only the 1st/2nd shift fork head can move.
4. Reverse mis-shift prevention mechanism
If the transaxle is shifted into reverse gear while the vehicle is running, this can break the clutch and the manual transaxle and at the same time lock up the tires, causing a very dangerous situation. Therefore, this mechanism is set up so that the driver must shift into the neutral position before shifting into reverse gear.
5. Operation of reverse mis-shift prevention mechanism
(1) When selecting the gear When the gear shift lever is moved to the 5th/reverse selection position (the neutral position between 5th and reverse gears), the shift inner lever No. 2 moves in the “5th/reverse” direction, turning the reverse restrict pin in the direction as shown by arrow A.
(2) Shifting into 5th gear When the transaxle has been shifted into 5th gear, shift inner lever No. 2 rotates in the direction shown by arrow B, releasing the reverse restrict pin. As a result, the reverse restrict pin is returned to its original position by a return spring.
(3) Attempted shifting from 5th gear into reverse If gear shifting is attempted directly from 5th gear into reverse (as shown by arrow C), the shift inner lever No. 2 hits the reverse restrict pin, preventing the transaxle from shifting into reverse from 5th gear.
(4) Shifting into reverse gear After the gear shift lever is once returned to the neutral position between 3rd and 4th gears and then moved to the 5th/reverse selection position, shift inner lever No. 2 and the reverse restrict pin will be in the configuration as shown in the left. In this configuration, shifting into reverse rotates shift inner lever No. 2 in the direction shown by arrow D without any interference from the reverse restrict pin.
6. Reverse one-way mechanism
The reverse idler gear moves only when the transaxle is shifted into reverse. When it is shifted into 5th gear, the reverse idler gear is kept in the neutral position.
Reverse one-way mechanism operation
(1) Shifting into 5th gear When the transaxle is shifted into 5th gear, the shift fork shaft No. 3 is moved to the right, causing balls to be pushed into the grooves of shift fork shaft No. 2.
(2) Shifting into reverse When the transaxle is shifted into reverse, the reverse shift fork is moved to the left by the snap ring which is fitted onto the shift fork shaft No. 3.
(3) Shifting from reverse into neutral The shift fork shaft No. 3, the balls and reverse shift fork are all moved integrally to the right.
7. Shift detent mechanism
There are three grooves on each shift fork shaft, and the detent ball is pushed into the groove by the spring when shifting gears. This not only prevents the transaxle from jumping out of gear, but also gives the driver a better feel for the gear engagement.
8. Hub sleeve function
To prevent the gear from jumping out, the spline between the hub sleeve and the speed gear is tapered to form a chamfer shape and improve the meshing of the hub sleeve and speed gear. For the same purpose, the teeth of the input, idler, and reverse gears are also slightly tapered.
(1) When the driving force is transmitted from a gear to the hub sleeve The splines on the gear mesh with all the hub sleeve splines.
(2) When the driving force is transmitted from the hub sleeve to a gear (during engine breaking) A lower number of gear splines meshes with the hub sleeve. This causes the meshing pressure of the hub sleeve and the gear to increase, thus preventing the transaxle from jumping out of gear.
SERVICE HINT:
If the hub sleeve spline chamfer portion is worn, the transaxle jumps outof gear.
9. Reverse detent mechanism
There is also a groove on the upper surface of the reverse shift fork into which the lock ball is pushed by a spring. When the transaxle is not shifted into reverse, this groove prevents the reverse idler gear from moving.