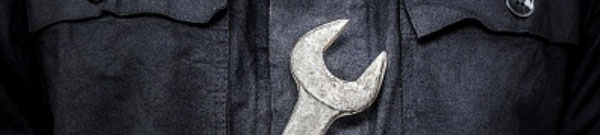
1. Line pressure optimal control
The ECT uses a throttle position sensor to detect the accelerator opening angle (load) and control the line pressure. The line pressure is controlled by using a linear solenoid valve (SLT). Through the use of the linear solenoid valve (SLT), the line pressure is optimally controlled in accordance with the engine torque information, as well as with the internal operating conditions of the torque converter and the transaxle. Accordingly, the line pressure can be controlled minutely in accordance with the engine output, traveling condition, and the ATF temperature, thus realizing smooth shift characteristics and optimizing the workload on the oil pump.
HINT:
For line pressure control, some models use the throttle cable in the same manner as the full hydraulically-controlled automatic transaxle.
SERVICE HINT:
If the solenoid valve (SLT) fails, the inner valve will be fixed at the top (Hi side), so there will be a greater shock during shifting.
2. Clutch pressure optimal control
Linear solenoid valve (SLT) is used for optimal control of clutch pressure. The ECU monitors the signals from various types of sensors such as the input turbine speed sensor, allowing linear solenoid valve (SLT) to minutely control the clutch pressure in accordance with engine output and driving conditions. As a result, smooth shift characteristics have been realized.
3. Clutch to clutch pressure control
When the automatic transaxle shifts, hydraulic pressure is released from one element and used for another. The clutch to clutch pressure control is adopted to make this process smooth. This control that the ECU sends a signal to the linear solenoid valve (SLT) and the hydraulic pressure applying on the back pressure side of the accumulator is optimized.
4. Engine torque control
Engagement of the clutches and brakes of the planetary gear unit in the transaxle is controlled smoothly by momentarily retarding the engine ignition timing when gears are shifting up or down in the transaxle. When the ECU judges a gear shift timing according to signals from various sensors, it activates the shift control solenoid valves to perform gear shifting. When the gear shifting starts, the ECU retards the engine ignition timing to reduce the engine torque. As a result, engagement force of the clutches and brakes of the planetary gear unit is weakened and the gear shift change is performed smoothly.
5. “N” to “D” squat control
When the transaxle is shifted from the “N” range to the “D” range, the squat control system prevents it from shifting directly into 1st gear, by causing it to shift into 2nd or 3rd gear first, and then into 1st gear. It does this in order to reduce shifting shock and squatting of the vehicle. Squat control functions only when all of the following conditions exist simultaneously.
Vehicle halted
Stop light switch ON
Transaxle being shifted from “N” range to “D” range
Coolant warmed-up
6. Shifting control in uphill/downhill driving
In a conventional automatic transaxle, when accelerating/decelerating on a hill, the gears will frequently shift depending on the conditions, which prevents smooth driving. To perform the shifting control in uphill/ downhill driving, the Engine & ECT ECU uses the throttle position sensor and speed sensor signals to select the optimum gear position. When the ECU determines to be climbing, shifting up to the O/D gear is restricted to achieve smooth driving. In addition, when the ECU determines to be descending and brake operation is detected, the transaxle is shifted down to the 3rd gear and engine braking is engaged.
HINT:
Hill climbing and descending is determined by comparing the actual acceleration calculated from the speed sensor signal with the standard acceleration stored in the ECUĆ fs memory.