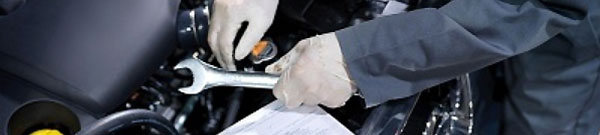
1. Overview
The V-belt driven cooling fan increases in fan speed in proportion to the increase in engine speed. For this reason, the fan speed of the cooling fan with the temperature control fluid coupling control the fan speed by sensing the temperature of the air flowing through the radiator. The temperature control fluid coupling contains a fluid clutch with silicone oil. The transfer of revolution to the fan via the V-belt is controlled by the adjustment of the amount of oil in the operating chamber. When the temperature is low, the rate of fan revolution is decreased helping with engine warm-up and preventing noise. When engine temperature is high, the fan revolution rate is increased to supply an adequate volume of air to the radiator, thereby increasing the cooling effect.
2. Operation
Air Temperature (HOT) during low speed driving
The fluid coupling shaft revolution is transferred to the fan as is.
Air temperature (HOT) during high speed driving
Fan revolution resistance increases and the fluid coupling slips to make the fan revolve at a rate slightly slower than the fluid coupling shaft.
Air temperature(WARM) during high speed driving
The bimetal plate switches the oil route and decreases the operation oil amount. This increases slippage of the operating chamber, resulting in an even further decreased rate of revolution.
Air temperature (COLD) during high speed driving
The oil route is switched and operation oil level further decreases. At this time slippage is greatest and the fan revolution rate is the least.
Electronically Controlled Hydraulic Cooling Fan System The electronically controlled hydraulic cooling fan system uses a hydraulic motor to turn the fan. The computer adjusts the amount of oil flowing to the hydraulic motor, so the fan revolves without stages and the fan speed can always be adjusted to achieve the most appropriate air volume. Compared to the electric fan, the motor is smaller and lighter in weight, and has the ability to supply a greater air volume. However, the oil pump and the control system are more complicated.
EngineCompression Pressure
1. Check compression pressure
Allow the engine to warm up and stop. Remove all spark plugs and crank the engine with the throttle valve fully opened in order to measure the compression pressure of all cylinders.
HINT:
Disconnect connectors of all injectors so that fuel cannot be injected.
Remove the igniter or disconnect connectors of the igniter so that a spark is not generated.
The fully charged battery should be used to obtain an engine speed of over 25rpm.
NOTICE:
This inspection must be performed in as short a time as
possible.
Example1NZ-FE engine (NZE12#)
Compression pressure1,471 kPa ( 15.kgf/cm2)
Minimum pressure1,07kPa ( 11.kgf/cm2)
Difference between each cylinder98 kPa ( 1.kgf/
cm2) or less
SERVICE HINT:
If the compression pressure is low, pour a small amount
of engine oil in the spark plug hole. Measure the compression pressure again.
When the compression pressure risesA piston ring or cylinder bore may be worn or damaged.
When the compression pressure stays lowA valve may be sticking, a valve seat may be improper, or there may be leakage from the gasket.