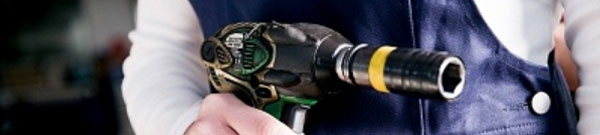
1. Description
The synchromesh mechanism is used to prevent “gear noise” and to make gear shifting smoother. This mechanism is called “synchromesh” because two gears which rotational speed is different are synchronized by friction force during gear shifting. Transaxles with synchromesh mechanism have the following advantages.
(1) They eliminate the need for the driver to “double clutch” (depressing the clutch pedal twice each time gears are shifted).
(2) When shifting gears, the power can be transmitted with less delay.
(3) Shifting can be carried out more smoothly without damaging the gears.
2. Key type synchromesh mechanism
(1) Construction
a. Each forward gear on the input shaft is engaged at all times with the corresponding gear on the output shaft. These gears rotate at all times even after the clutch is engaged because they are not fixed on the shaft and run idle.
b. The clutch hubs mesh with shafts by splines inside the clutch hub. Furthermore, the hub sleeve meshes with the outer circumference spline of the clutch hub and can move to the axial direction.
c. The clutch hub has three grooves in the axial direction, and the shifting keys enter the grooves. The shifting key is pushed against the hub sleeve at all times by the key spring.
d. When the gear shift lever is in the neutral position, the protrusion of each shifting key fits inside the slot in the hub sleeve.
e. A synchronizer ring is located between the clutch hub and the cone of the speed gears and is pushed against one of these cones. Small grooves are provided over the entire conical area inside of the synchronizer ring to improve friction. Furthermore, the ring also has three grooves for the shifting keys to fit into.
(2) Operation
a. Neutral
Each speed gear is meshed with the corresponding driven gear and run idle on the shaft.
b. Start of synchronization
As the shift lever is moved, the shift fork, which is fitted in a groove in the hub sleeve, moves in the direction indicated by the arrow. Since the protrusion at the center of the shifting key is fitted to the hub sleeve groove, the shifting key also moves to the arrow direction at the same time, and pushes the synchronizer ring to the speed gear cone portion, resulting in the synchronization start.
c. Midway through synchronization
When the shift lever is moved further, the force which is applied to the hub sleeve overcomes that of the shifting key spring and the hub sleeve rides up into the protrusion of the key.
d. End of synchronization
The force being applied to the synchronizer ring becomes even stronger and pushes the speed
gear cone portion. This causes the speed of the speed gear to be synchronized with that of the hub sleeve.
When the speeds of the hub sleeve and the speed gear become equal to each other, the synchronizer ring begins rotating slightly in the rotation direction. As a result, the hub sleeve splines mesh with the synchronizer ring splines.
e. End of shift change
After the hub sleeve spline meshes with synchronizer ring spline, the hub sleeve moves further and meshes with the speed gear spline. Then, the shift change ends.
SERVICE HINT:
If the inner circumference of the synchronizer ring and the speed gear cone portion become worn, both speeds cannot be in sync. Abnormal noise occurs or it becomes difficult to shift gears.