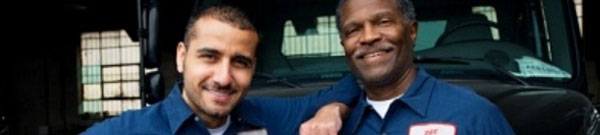
1. TRC operation (for pressure increasing mode)
When the accelerator is depressed, the hydraulic pressure for each wheel cylinder is controlled to control the drive wheel slip. At this time, in models with a precharge function, the precharge solenoid valve operates to also use the hydraulic pressure from the master cylinder. A linear solenoid valve is used for the master cylinder cut solenoid valve. The hydraulic pressure is linearly controlled to smooth out hydraulic pressure fluctuations by adjusting the amount of current flowing in the solenoid valve as controlled by the ECU.
2. VSC operation
The VSC controls the brake hydraulic pressure by controlling the transmission to each wheel cylinder of the hydraulic pressure generated by the pump inside the brake actuator to control the front wheel skid or rear wheel skid. At this time, in models with a precharge function, the precharge solenoid valve operates to also use the hydraulic pressure from the master cylinder.
(1) During front wheel skid suppression control When turning right, the front wheel skid suppression control operates the right and left front wheel brakes and the brake of the inner rear wheel. The brake control method (controlled wheels) for the various wheels differs depending on the model (FF, FR).
(2) During rear wheel skid suppression control When turning right, the rear wheel skid suppression control operates the brakes of the outbound front wheel and, if necessary, the outer rear wheel. The brake control method (controlled wheels) for the various wheels differs depending on the model (FF, FR).
Hydraulic Brake Booster General Construction
While a regular brake booster uses the engine vacuum to generate a large hydraulic pressure, the hydraulic brake booster is a device that uses a pump motor to generate a large hydraulic pressure to reduce the required brake depression force. The hydraulic brake booster consists of the master cylinder, brake actuator, reservoir tank, pump, pump motor, and accumulator. To inspect the reservoir fluid level, turn the ignition switch to OFF and release the pressure in the power supply system.
HINT
When a pressure in power supply system is released, reaction force becomes heavy and stroke becomes shorter. The master cylinder brake booster consists of a brake booster portion, master cylinder portion, and regulator portion. These are positioned coaxially to achieve a simple and compact construction.
The brake booster portion consists of an operation rod, power piston and booster chamber.
The master cylinder portion consists of a master cylinder piston, return spring and center valve.
The regulator portion consists of a regulator piston, return spring, spool valve, reaction rod, and rubber reaction disc. Hydraulic Circuit
1. Pressure increase (Low pressure)
(1) The pedal operation force transmits as followsOperation Rod –> Power Piston –> Master Cylinder Piston
(2) The load setting of the master cylinder’s return spring is higher than that of the regulator piston’s return spring, the regulator piston gets pushed before the volume in the master cylinder becomes compressed.
(3) The spool valve closes the port A(between the reservoir tank and booster chamber) and opens the port B(between the reservoir tank and accumulator). Then, the pressurized brake fluid is introduced into the booster chamber to provide a power assist to the pedal effort.
(4) This time, the power assist overcomes the force of the master cylinder’s return spring. This causes the volume in the master cylinder to become compressed and increased the pressure that is applied to the front brakes. At the same time, the pressure in the booster chamber increases the pressure that is applied to the rear brakes. During the initial stage of the brake operation, the booster pressure that is applied to the rubber reaction disc is small. Therefore, a return force in the rightward direction does not apply to the spool valve via the reaction rod.