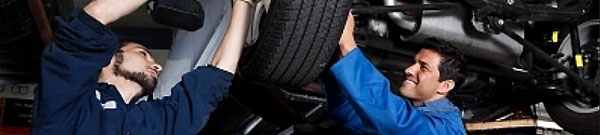
The sensors convert various information into voltage change that can be detected by the engine ECU. There are many types of sensor signals, but there are five main types of methods for converting the information into voltage. Understanding the characteristics of these types makes it possible to determine during measurement if the terminal voltage is correct or not.
1. Using VC voltage (VTA, PIM)
A5V constant voltage (VC voltage) for operating the microprocessor is created inside the engine ECU by the battery voltage. This constant voltage, which is supplied as the sensor power source, is the VC terminal voltage. In this type of sensor, a voltage (5 V) is applied between the VC and E2 terminals from the constantvoltage circuit in the engine ECU as shown in the illustration. Then, this sensor substitutes the detected throttle valve opening or the intake manifold pressure for the voltage change between and 5 V in order to output.
SERVICE HINT:
If the constant-voltage circuit malfunctions or the VC circuit shorts, the power supply to the microprocessor will be cut-off, causing the engine ECU to stop functioning and the engine to stall.
2. Using a thermistor (THW, THA)
A thermistor’s resistance value changes in accordance with the temperature. For this reason, thermistors are used in such devices as the water temperature sensor and intake air temperature sensor, to detect changes in temperature. As shown in the illustration, voltage is supplied to the sensor thermistor from the constant-voltage circuit (5 V) in the engine ECU via resistor R. The properties of the thermistor are used by the engine ECU to detect the temperature using the change in voltage at point A in the illustration. When the thermistor or wire harness circuit is open, the voltage at point A becomes 5 V, and when there is a short from point A to the sensor, the voltage becomes V. Therefore, the engine ECU will detect a malfunction using the diagnosis function
3. Using voltage ON/OFF
(1) Devices using a switch (IDL, NSW) When the voltage turns ON and OFF, it causes the sensor to detect the switch ON/OFF condition. A voltage of 5 V is applied to the switch by the engine ECU. The engine ECU terminal voltage is 5 V when the switch is OFF, and V when the switch is ON. The engine ECU uses this change in voltage to detect the sensor condition. In addition, some devices use a battery voltage 12 V.
(2) Devices using a transistor (IGF, SPD) This is a device that uses transistor switching instead of a switch. As with the above device, the turning ON and OFF of the voltage is used to detect the sensor operation condition. As with devices that use a switch, a voltage of 5 V is applied to the sensor from the engine ECU, and the engine ECU uses the change in terminal voltage when the transistor turns ON or OFF to detect the condition of the sensor. In addition, some devices use a battery voltage 12 V.
4. Using a power supply other than from the engine ECU (STA, STP)
The engine ECU determines whether another device is operating by detecting the voltage that is applied when another electrical device is operating. The illustration shows a stop lamp circuit, and when the switch is ON, a battery voltage 12 V is applied to the engine ECU terminal, and when the switch is OFF, the voltage becomes V.
5. Using voltage generated by the sensor (G, NE, OX, KNK)
As the sensor generates and outputs power itself, a voltage does not need to be applied to the sensor. The engine ECU determines the operation condition by the voltage and frequency of the generated power.
HINT:
When inspecting the engine ECU terminal voltage, the NE signal, KNK signal and etc. are output in an AC waveform. Therefore, highly accurate measurements can be taken using an oscilloscope.