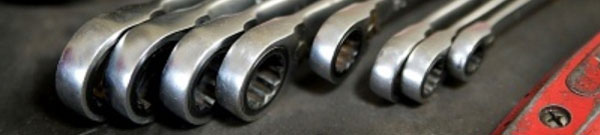
The drive train transmits the power of the engine to the wheels. It is broadly divided into the following classifications:
1. FF (Front engine-Front wheel drive vehicle)
The drive force from the engine is transmitted via the transaxle differential to the left and right drive shafts, wheels, and tires.
2. FR (Front engine-Rear wheel drive vehicle)
The drive force from the engine is transmitted from the transmission and then via the propeller shaft and differential to the right and left drive shaft (or axle shaft), axle shaft, wheels, and tires.
HINT:
The drive shaft and axle shaft combination is also called the drive shaft.
Differential Construction
The differential further increase the torque transmitted via the transmission and distributes the drive force to the left and right drive shafts. In addition, this is also a differential gear that generates the difference in the rotational speed between the inner wheel and outer wheel during cornering, and allows the smooth driving on curves.
1. Final gears
The final gears reduce the rotation from the transaxle (transmission) to increase the torque. The FR vehicle final gears increase the torque while changing its direction.
2. Differential gears
The differential gears create two different wheel turning speeds when the vehicle is driving on curves.
1. FF vehicle differential
The differential used in FF vehicles with transversely-mounted engines is integrated with the transmission. The differential assembly is mounted in between the transmission case and the transaxle case. A helical gear is used for the ring gear. This gear is integrated with the differential case and is mounted on the transaxle via two side bearings. The drive shaft meshes with the splines inside the side gear. There are ordinarily two pinion gears, but in differentials for high-power engines, four pinion gears are often used.
2. FR vehicle differential
The final gear and the differential gear in an actual product are assembled as a unit, as shown, and installed directly in the differential carrier, which is further fitted to the rear axle housing, body, or frame. The universal joint of the propeller shaft is fixed to the companion flange, and rotates the drive pinion through the companion flange. The drive pinion is fitted to the differential carrier by two tapered roller bearings. The ring gear and the differential case are integrally fitted to the differential carrier via two side bearings. The drive pinion and the ring gear are hypoid gears for which the shaft extensions are mutually offset, so special hypoid gear oil must be used to lubricate them. The side gear and the rear axle shaft are fitted to each other via splines.
3. Adjustment
(1) Side bearing preload adjustment
A taper roller bearing is used in the side bearing, so preload adjustment is required.
(2) Drive pinion preload adjustment
The preload of the drive pinion bearings is normally adjusted by changing the distance of the front and rear inner races while the outer races are fixed to the differential carrier. This can also be achieved by changing the total thickness of shims used, or applying pressure to the collapsible spacer (by tightening the nut) in order to alter its length.
(3) Hypoid gear backlash adjustment
The backlash adjustment performs to adjust the clearance of the contact surface between the drive pinion and ring gear. When the backlash is large, the differential case is adjusted toward to the drive pinion, and when the backlash is small, it is adjusted away from the drive pinion. The adjustment nut is used to make the adjustment.
(4) Hypoid gear tooth contact adjustment
The hypoid gear tooth contact is adjusted by offsetting the drive pinion and ring gear use the adjusting washer.
SERVICE HINT:
1. Side bearing preload
The thrust load is received from the ring gear, so if the preload adjustment is poor, the side bearing taper roller will wear causing unstable rotation. To prevent this, the preload adjustment using the adjusting shim or adjusting nut is required.
2. Drive pinion preload (FR)
The thrust load is received from the ring gear, so if the preload adjustment is poor, the taper roller bearings on both ends of the drive pinion will wear causing unstable rotation. To prevent this, the preload adjustment using the adjusting shim or collapsible spacer is required.
3. Hypoid gear backlash (FR)
The ring gear generates a thrust load, which is received by the drive pinion, so if the backlash adjustment is poor, an excessive force will be applied, causing damage to the teeth of both gears and seizing. It is required to adjust the adjusting nut or adjusting shim, and adjust the backlash.
4. Hypoid gear tooth contact (FR)
The ring gear generates a thrust load, which is received by the drive pinion, so if the tooth contact adjustment is poor, an excessive force will be applied, causing damage to the teeth of both gears and seizing or noise to occur be generated. Not only the backlash, but also the mutual tooth contact must be adjusted with the adjusting washer.
Operation
1. When driving straight
When driving straight, an even resistance is applied to both the right and left wheels, so the ring gear, pinion gear, and side gear rotate as a single unit so that the drive force is transmitted to both wheels.
2. When driving on a curve
When driving on a curve, the rotational speed is different between the outer tire and inner tire. In other words, inside the differential the inner B side gear turns slowly and the pinion gear rotates so that the outer A side gear rotates faster. This is how the differential allows the vehicle to drive smoothly through curves.
HINT:
The operation of the differential works to apply the same torque to both the right and left wheels. So while this has the advantage of making driving through curves smooth, it has the disadvantage of reducing the drive force to both wheels when the drive force is reduced to one wheel.