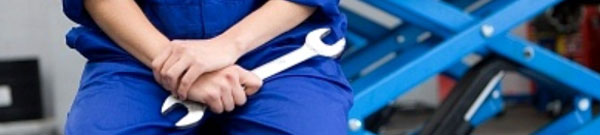
1. Outline
In automotive suspension systems, the springs used are metallic springs and non-metallic springs
- Metallic springs
- Leaf springs
- Coil springs
- Torsion bar springs
- Non-metallic springs
- Rubber springs
- Air springs
2. Leaf springs
Leaf springs are made of a number of curved bands of spring steel, called “leaves”, stacked together in order from shortest to longest. This stack of leaves is fastened together at the center with a center bolt or a rivet and to keep the leaves from slipping out of place, they are held at several places with clips. Both ends of the longest (main) leaf are bent to form spring eyes, used to attach the spring to the frame or to a structural member such as a side member. Generally, the longer a leaf spring, the softer it will be. Also, the more leaves in a leaf spring, the greater the load they will withstand, but on the other hand, the spring will become firmer and riding comfort will suffer.
Characteristics:
- Since the springs themselves have adequate rigidity to hold the axle in the proper position, it is not necessary to use linkages for this.
- They function to control their own oscillation through inter-leaf friction.
- They have sufficient durability for heavy-duty use.
- Due to inter-leaf friction, it is difficult for them to absorb the minute vibrations from the road surface. Therefore leaf springs are generally used for large commercial vehicles which carry heavy loads and for which durability is highly regarded. The curvature of each leaf is called “nip”. Since the nip of a leaf is greater the shorter the leaf, each leaf curves more sharply than the one above it in the stack. When the center bolt is tightened, the leaves flatten somewhat, as shown in the illustration in the left, causing the ends of the leaves to press very tightly against one another. The overall curvature of the leaf spring is called “camber”. However, this friction also causes a decrease in riding comfort, since it prevents the spring from flexing easily.
The purpose of nip
- When a spring is flexed, nip causes the leaves in the spring to rub together, and the friction created by this rubbing quickly damps the oscillations of the spring. This friction is called inter-leaf friction, and is one of the greatest features of the leaf spring. However, this friction also causes a decrease in riding comfort, since it prevents the spring from flexing easily. Therefore, leaf springs are mainly used on commercial vehicles.
- When the spring rebounds, nip prevents gaps from occurring between each of the leaves, thus preventing dirt and sand, etc., from penetrating between the leaves and causing wear.
- Measure to reduce inter-leaf friction Silencer pads are inserted between each of the leaves at their ends to improve the sliding of the leaves against each other. Each of the leaves is also tapered at the ends so that they exert the proper amount of pressure when they come in contact with each other. Helper springs In trucks and many other vehicles which undergo great fluctuations in their loads, helper springs are used. The helper spring is installed above the main spring. When the load is light, only the main spring operates, but when the load exceeds a certain value, both the main and helper springs come into operation
3. Coil springs
Coil springs are made from rods of special spring steel formed into the shape of a coil. When a load is placed on a coil spring, the entire rod is twisted as the spring contracts. In this way, the energy of the external force is stored, and shock is cushioned.
Characteristics:
- The energy absorption rate per unit of weight is greater in comparison with leaf springs.
- Soft springs can be made.
- Since there is no inter-leaf friction as with leaf springs, there is no control of oscillation by the spring itself, so it is necessary to use shock absorbers along with them.
- Since there is no resistance to lateral forces, linkage mechanisms to support the axle (suspension arm, lateral control rod, etc.) are necessary Progressive spring If a coil spring is made from a rod of spring steel having a uniform diameter, the entire spring will flex uniformly in proportion to changes in the load. This means that if a soft spring is used, it will not be stiff enough to handle heavy loads, while if a hard spring is used, it will give a rough ride when only lightly loaded. However, if a rod having a constantly-changing diameter is used, as shown in the left, the ends of the spring will have a lower spring rate than the center. Consequently, under light loads, the ends of the spring will contract and absorb road shock. On the other hand, the center part of the spring will be stiff enough to handle heavy loads. Unequal-pitch spring, conical springs, etc. have the same effect.