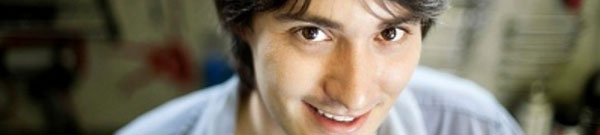
2.Twin-tube type
Inside the absorber shell (outer tube) there is a cylinder (pressure tube), and inside that there is a piston which moves up and down. At the base of the piston rod, a piston valve is installed which generates damping force when the shock absorber is extended (during rebounding). At the bottom of the cylinder there is a base valve which generates damping force when the shock absorber is compressed (during bounding). The inside of the cylinder is filled with absorber fluid, but only 2/3 of the reservoir chamber is filled with fluid, the rest being filled with air at atmospheric pressure or low-pressure gas. The reservoir serves as a storage tank for the fluid entering and leaving the cylinder Low-pressure gas-filled type is filled with gas under low pressure (0.3-0.6 MPa; 3-6 kgf/cm2 ; 43-85 psi). This prevents the generation of abnormal noise due to cavitation and aeration that can occur in shock absorbers using only fluid. Minimization of cavitation and aeration also makes it possible to obtain a more stable damping force, thus improving riding comfort and handling stability. In some low-pressure gas-filled shock absorbers, the base valve is eliminated so that damping force is generated during both bounding and rebounding by the piston valve.
HINT:
Cavitation:
When the fluid flows at high speed within the shock absorber, the pressure will drop in some areas, forming air pockets or cavities in the fluid. This phenomenon is called cavitation. These cavities collapse when carried into regions of high pressure, resulting in great impact pressure. This will generate noise, cause pressure fluctuations, and can damage the shock absorber itself.
Aeration: Aeration is the mixing of air with shock absorber fluid. This can lead to noise, pressure fluctuations, and pressure loss.
Operation
<1>During bounding (compression)
Piston rod’s speed of motion high When the piston moves downward, the pressure in chamber A under the piston becomes high. The fluid pushes open the non-return valve of the piston valve, and with practically no resistance flows into chamber B (damping force is not generated). At the same time, an amount of fluid equal in volume to the volume of the fluid displaced by the piston rod as it is pushed into the cylinder, is forced through the leaf valve in the base valve and flows into the reservoir chamber. It is at this time that damping force is generated by the flow resistance.
Piston rod’s speed of motion low If the speed of the piston rod is very low, the nonreturn valve in the piston valve and the leaf valve in the base valve will both remain closed because the pressure in chamber A is low. However, since there are orifices in the piston valve and the base valves, the fluid in chamber A flows through them into chamber B and the reservoir chamber, so that only a slight damping force is generated. <2>During rebounding (expansion)
Piston rod’s speed of motion high When the piston rod is moving upward, the pressure in chamber B above the piston becomes high and the fluid inside chamber B opens the leaf valve in the piston valve and flows into chamber A. At this time, the flow resistance of the fluid acts as a damping force. Since the rod moves upward, a portion of it moves out of the cylinder, so the volume of fluid displaced by it decreases. To compensate for this, the fluid passes through the non-return valve of the base valve from the reservoir chamber and flows with practically no resistance into chamber A.
Piston rod’s speed of motion low When the piston rod is moving at a low speed, both the leaf valve in the piston valve and the non-return valve in the base valve remain closed because the pressure in chamber B above the piston is low. Therefore, the fluid in chamber B passes through the orifices in the piston valve and flows into chamber A. Also, the fluid in the reservoir chamber passes through the orifice in the base valve and flows into chamber A, so only a slight damping force is generated.