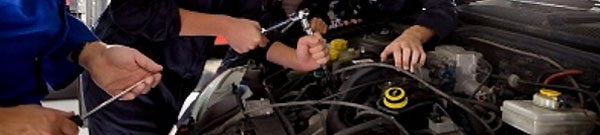
What is brake squeaking?
Brake squeaking is a vibrated symptom caused by the friction between the pads and rotor. This vibration is transmitted as a sound. This symptom is referred to as “self-excited vibration,” and differs from the “forced vibration,” such as body vibration. Self-excited vibration produces a further vibration to itself and as the vibration becomes stronger, the energy becomes greater.
Sound generation and how the sound is transmitted
Brake squeaking is compared to a howling phenomenon. The howling phenomenon is produced by the following process: a sound enters the microphone from the speaker, amplified by the amplifier, repeatedly comes out of the speaker, and finally becomes louder sound. If this symptom is compared to a brake, it is as follows. Speaker: rotor Microphone: pads Volume level of amplifier: coefficient of pad friction Distance between the microphone and the speaker: attenuation (effectiveness of the shims)
Construction of Brake and Brake Squeaking
In the case of self-excited vibration, once a vibration is generated, the vibration is amplified and it becomes greater. As the amplitude becomes larger, greater attenuation will be required to stop the vibration. In the brake construction, pads and the rotor contact closely, so it is difficult to attenuate the vibration.
Generated frequency
In the case of brake squeaking, the generated frequency varies. Even if brake squeaking at a certain frequency is reduced, another brake squeaking will be generated at different frequency. The frequency varies depending on the model and it is difficult to reduce anything more than the general vibration. The effectiveness of the reduction sometimes appears, but sometimes it does not appear.
The relationship between the brake squeaking and the brake
Brake squeaking is generated by the friction between the pads and the rotor, so there is a correlation between the pad friction coefficient and brake squeaking. Therefore, the prevention of brake squeaking and the improvement of brake effectiveness are rather difficult to achieve at the same time. In fact, a large amount of energy is transmitted to the rotor in the pads that are effective, the brake squeaking tends to occur. Conditions that tends to cause brake
squeaking
• When the vehicle is left or the brake is cooled
Brake squeaking tends to occur due to the increase of the brake pad friction coefficient caused by the oxidation of the rotor and pads surfaces, or pad moisture coef absorption. Fi absorption.
• When the brake is cooled down under high temperature conditions
When the temperature of the pad is over 200 degrees centigrade, the resin inside the pads decomposes and the pad surface loses its abrasiveness. When the temperature then drops, the friction coefficient increases. As a result, the brake squeaking tends to occur.
When the temperature of the pad becomes high, the paint on the sides sometimes become whitish, helping to judge the thermal history.
• When the rotor ground trace cannot be seen
When the abrasive chips of the pad attaches to the rotor surface, the rotor surface is ground by the pads, accordingly. When the surface irregularity decreases, the friction coefficient increases. As a result, the brake squeaking tends to occur.
Brake squeaking reproduction test
• Perform this test by altering the pedal depressing force on a slope.
• Increase the brake temperature and leave it for 30 minutes. Then perform this test.
• Leave the brake overnight to decrease the brake temperature. Then perform this test.
Brake Squeaking Reducing Method
• Inspection of the anti-squeal shim and application of
grease
Check for peeling or warping of rubber on the anti-squeal shim surface. Apply grease to the grease pan and claw of the anti-squeal shim. By using grease, this procedure improves the attenuation force and changes the contact between the calliper and pad.
• Piston back
Press the piston of the calliper back once. In this procedure, correcting the gouging of the piston and sliding it smoothly helps to maintain the stable contact of the pads.
• Pad backing inspection and repair
Check for warping of the pad backing. If warping is found, grind the backing. This procedure helps to even the contact of the piston and calliper claw to the pads.
• Pads torque reception surface fi le and grease application
Check the contact truck. If the pads contact unevenly, fi le the surface with sandpaper to correct it so that it evenly contacts with the calliper mounting. Apply grease to the torque reception surface. This procedure helps to reduce the friction to the torque reception surface and to make the pad stable.