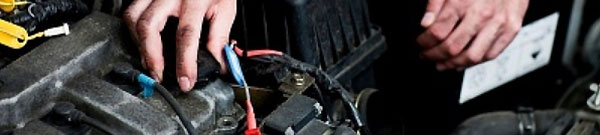
Conventional EFI-diesel
Common-rail EFI-diesel
4. Comparison of the target injection timing and the actual injection timing
As with the convention EFI-diesel, the basic injection timing of the common- rail EFI-diesel is determined through the engine speed and the accelerator pedal opening angle, and by adding a correction value based on the water temperature and the intake air pressure (volume). The ECU sends injection signals to the EDU and advances or retards the timing to adjust the injection starting timing.
Starting Control
Injection Volume Control During Starting
The starting injection volume is determined by adjusting the basic injection volume in accordance with the starter ON signals (ON time) and coolant temperature sensor signals. When the engine is cold, the coolant temperature will be lower and the injection volume will be greater. To determine the starting injection timing is corrected in accordance with the starter signals, water temperature and engine speed. When the water temperature is low, if the engine speed is high, the injection timing is advanced.
Injection Rate Control
Split Injection
A radial plunger type pump performs split injection (two-time injection) when starting the engine at an extremely low temperature (or under -10 degrees) to improve startability and reduce the generation to white and black smoke.
Pilot Injection
The common-rail EFI-diesel uses pilot injection. In the pilot injection system, a small amount of fuel is initially injected before the main injection. When the main injection starts, the fuel that has been injected in advance is already ignited, enabling the fuel of the main injection to ignite smoothly.
Idle Speed Control
Based on the signals from the sensors, the ECU calculates the target speed in accordance with the driving conditions. The ECU then compares the target value with the (engine speed) signal from the engine speed sensor and controls the actuators(SPV/injector) to regulate the injection volume in order to correct the idle speed. The ECU effects idle-up control (in order to improve the engine’s warm-up performance) during fast idle when the engine is cold, or during air conditioner/power heater operations. Also, in order to prevent fluctuations in idle speed caused by a reduction in engine load that occurs when the A/C switch is turned off, the volume is automatically corrected before the engine speed fluctuates.
Idle Vibration Reduction Control
This control detects the fluctuations in the engine speed during idle caused by the variances in the injection pump or nozzles, and corrects the injection volume for each cylinder. Consequently, idle vibration and noise are reduced.