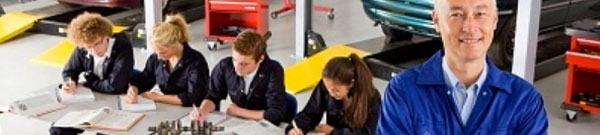
The lock-up clutch mechanism connects the engine power directly and mechanically to the automatic transaxle. Since the torque converter uses the fluid flow to transmit the power indirectly, there are power losses. Therefore, the clutch is attached in the torque converter to connect the engine and transaxle directly to reduce power loss. When the vehicle reaches a certain speed, the lock-up clutch mechanism is used to raise the power performance and fuel efficiency. The lock-up clutch is installed on the turbine runner hub, in front of the turbine runner. The damper spring absorbs the torsional force upon clutch engagement to prevent the generation of shock. A friction material (the same type that is used in the brakes and on the clutch disc) is bonded to the converter case or lock-up piston of the torque converter to prevent slippage at the time of clutch engagement.
Operation
When the lock-up clutch is actuated, it rotates together with the pump impeller and turbine runner. Engaging and disengaging of the lockup clutch is determined by changes in the direction of the hydraulic fluid flow in the torque converter when the vehicle reaches a certain speed.
1. Disengaging
When the vehicle is running at low speeds, the pressurized fluid (converter pressure) flows to the front of the lock-up clutch. Therefore, the pressure on the front and rear sides of the lock-up clutch become equal, so the lock-up clutch disengages.
2. Engaging
When the vehicle is running constantly at medium or high speed (generally above 60 km/h), the pressurized fluid flows to the rear of the lock-up clutch. Therefore, the converter case and lock-up clutch are directly connected. As a result, the lock-up clutch and converter case rotate together (For example, the lock-up clutch is engaged).